Coyuchi shows why it’s so hard to source organic, U.S. cotton
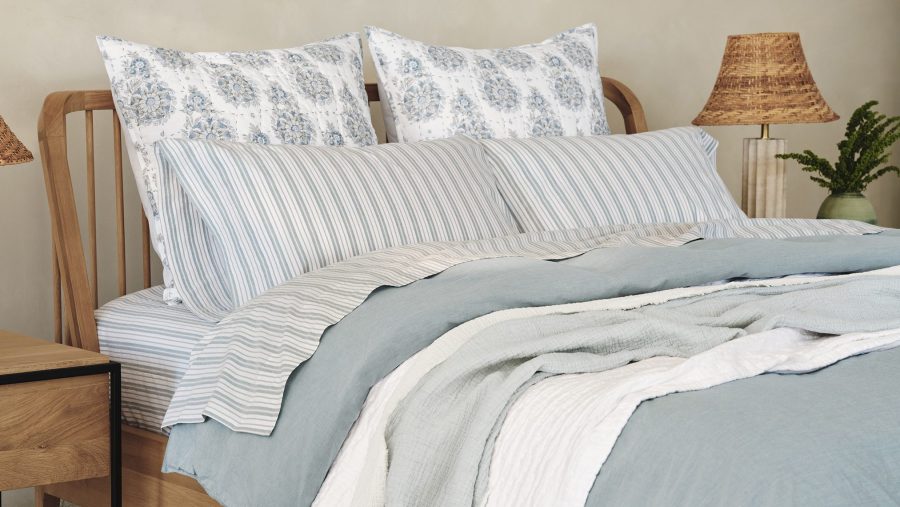
Bedding brand Coycuhi specializes in organic cotton bedsheets. And while the United States is one of the world’s biggest exporters of cotton, director of sourcing and sustainability Margot Lyron said the company has found it difficult to source and manufacture domestically. At present, no more than 1% of what Coyuchi can source is grown in this country.
“Sourcing in the U.S. has been one of our goals since I’ve been at the company, but there’s a plethora of challenges to that,” she said.
As new tariff policies disrupt global supply chains, much talk has turned to what’s possible in the realm of U.S. manufacturing and nearshoring. But for brands looking for cotton textiles, there are currently few industrial resources to tap, even as the country continues to have a healthy supply of raw cotton.
Data from the U.S. Department of Agriculture shows that the U.S. is estimated to export around 12 million bales of cotton this year, making up over a quarter of the overall share traded globally. Typically, China is the biggest buyer of U.S. cotton. But this supply chain is likely to see disruptions under new tariff policies. As companies based here are paying more for imported goods and finished products under President Donald Trump’s new tariff policies, China imposed a 15% retaliatory tariff on exports of certain U.S. agricultural products, including cotton. Cotton futures subsequently traded at their lowest levels in five years, per The Wall Street Journal.
Issac Hetzroni, a supply chain consultant known on TikTok as The Sourcing Guy, said people are often surprised to learn how much of the world’s cotton comes from the U.S. While there are some textile manufacturing hubs, such as downtown Los Angeles, most of the raw materials grown in the U.S. don’t stay here because there aren’t many spinning mills or manufacturing facilities to turn it into usable fabric.
“It is most likely shipped to Pakistan, or shipped to China or Vietnam,” he said, “because it’s just it’s so hard for us to process it, or cut and sew it. It’s very expensive to do that aspect of it [in the United States], so it’s not economical.”
Efforts are underway from trade associations like American Circular Textiles to push for expanded domestic manufacturing in the United States. But it could take decades, or even generations, to allow brands that use cotton to nearshore their production. So for now, any companies looking to nearshore their textile manufacturing are likely to run into the same roadblocks Coyuchi has faced.
Coyuchi, founded in 1991, was an early leader in the organic bedding category and has since expanded to other textiles like towels, blankets and mattresses. Organic cotton is known for using less water and fewer emissions, in addition to being free of synthetic pesticides. But as Lyons from Coyuchi explained, the amount of organic cotton farming in the U.S. is small in comparison to conventional. What’s more, there aren’t many spinning mills left to process the raw cotton into yarn.
Lyons had been working with a U.S. supplier of extra-long staple cotton that would also be spun into yarn in the U.S. But then the spinning mill shut down because the weaver retired. Because the mill shut down, it no longer made sense to use the U.S. source. “Then we were only spinning overseas, and the overseas unit was like, ‘Well, why are we going to buy U.S. cotton? We can buy the extra-long staple cotton for less money elsewhere,'” Lyons said.
Additionally, Lyons said the domestic manufacturing capacity for large linens is rather limited. There’s little infrastructure to process and manufacture cotton in the U.S. overall, let alone for products the size and scale of bedsheets. There could also be challenges making sheets in colors or patterns, Lyons said.
“A lot of the machines we would need are no longer here,” she said. “And you would need investment in not only the physical buildings and the machinery, but also the people who could run those facilities.”
Lyons said Coycuhi works directly with the farms or family businesses that make these products. But she said even that can be getting harder to come by.
“What we’re starting to see is partners getting to retirement age and no one to take over,” she said. “We recently had somebody retire and had to sell off their looms. They found a buyer for one of the looms, but not for another.”
In the meantime, brands are continuing to look overseas even as new tariff policies take hold. Hetzroni said Egyptian cotton is in high demand and can be priced competitively. He said it also makes sense for brands to diversify their supply chain out of China, and look to Latin America, Africa or other markets. But that, too, can come with big cost commitments of millions of dollars and may only be accessible for larger companies. And while the future may hold more U.S. manufacturing, he imagines it might look different than what current operations are.
“We’re going to be doing more and more nearshoring and then U.S.-based manufacturing over the next 20 years, but my honest viewpoint on it is that the way that’s going to happen is through more automation and robotics,” he said. “It’s not going to bring more blue-collar jobs back to the U.S., but it will bring more industry and the jobs surrounding the industry of manufacturing.”